BOLOGNA, Italy – With a more than consolidated partnership lasting 50 years, IMA and Coind fully embody the meeting of two top representatives in the Emilian Food and Packaging Valley. Both founded in 1961, the two Bolognese companies share views and objectives such as reliability, high quality and high technology for the best customer satisfaction, sustainability and social commitment.
The alliance dates back to the late sixties with the supply of the first IMA equipment forpackaging tea in filter bags, later boosted by the supply of coffee packaging solutions from 2005 on.
Coind is a leading Italian industrial group based just outside Bologna, in Emilia Romagna, with a total annual turnover of 78 million euro (up 10.5% on 2019) and more than 230 employees. The coffee division was founded in 1961, and is today one of Italy’s largest roasteries with over 7,000 tons of raw coffee beans roasted to serve seven million Italian families every year. With a wide range of products, from ground coffee and beans to coffee pods and single-serve capsules, Coind covers more than 60% of Italian private label production and has distributors in over 60 countries.
When Coind carried out an important production upgrade involving complete packaging lines for Nespresso® and Dolce Gusto® compatible capsules, including solutions from coffee filling to final product palletization, it chose IMA Coffee.
The latest IMA Coffee machine installed in the Coind plant is a 595 for aluminium capsules. Capable of processing up to 450 capsules per minute, this high-speed solution will theoretically handle 120 to 130 million capsules per year. Its ergonomic cantilever design ensures great accessibility for maintenance, service and easy cleaning thanks to the pull-out operating system, significantly reducing line downtimes.
Accurate product dosing is made possible thanks to precise and extremely gentle product handling to suit a wide range of products to be filled (coffee with different densities, tea and soluble powders). Excellent product quality is guaranteed by an on-line weighing system for each filled capsule, with data feedback to automatically adjust the dosing unit, and by vision systems for lid positioning.
We interviewed Luca Cioffi, President & CEO, and Valentina Pareschi, E-commerce & Communication manager,to understand how Coind finds working with IMA.
What is Coind’s vision of market trends, with regard to capsule and carton types and in terms of materials? What is your plan for the medium and long term?
The last few years have been marked by a major new topic, sustainability, which is becoming increasingly important on the Italian and international scene. It’s an issue that has also influenced the coffee capsule market and the materials used for their packaging.
As for the capsules, we are introducing two different responses to the “no plastic” trend: compostable, 100% recyclable capsules that can be disposed of in organic waste, and aluminium capsules, which we expect to be disposed of soon in dedicated collection centres.
There are some new introductions also with regard to formats: more and more brands, and retail distribution players too, are oriented towards maxi-formats of 30, 40 or 50 capsules, designed both for consumer convenienceas well as for lower consumption of packaging.
As a company, we have responded to these market demands by investing into production lines capable of making both types of capsules, with different packaging configurations; we are talking about about 20 million euros over the last three years.
At the same time, we are also taking action regarding the materials used for our boxes: for more than a year all our cardboard has been FSC (Forest Stewardship Council) certified, i.e. the raw material used derives from responsible forest management, with traceable and documentable origin.
These are only a small part of the initiatives implemented by Coind to reduce its impact on the environment. Our medium and long-term perspective is certainly to continue investing into sustainable solutions in terms of product, packaging and certifications, in line with market requirements.
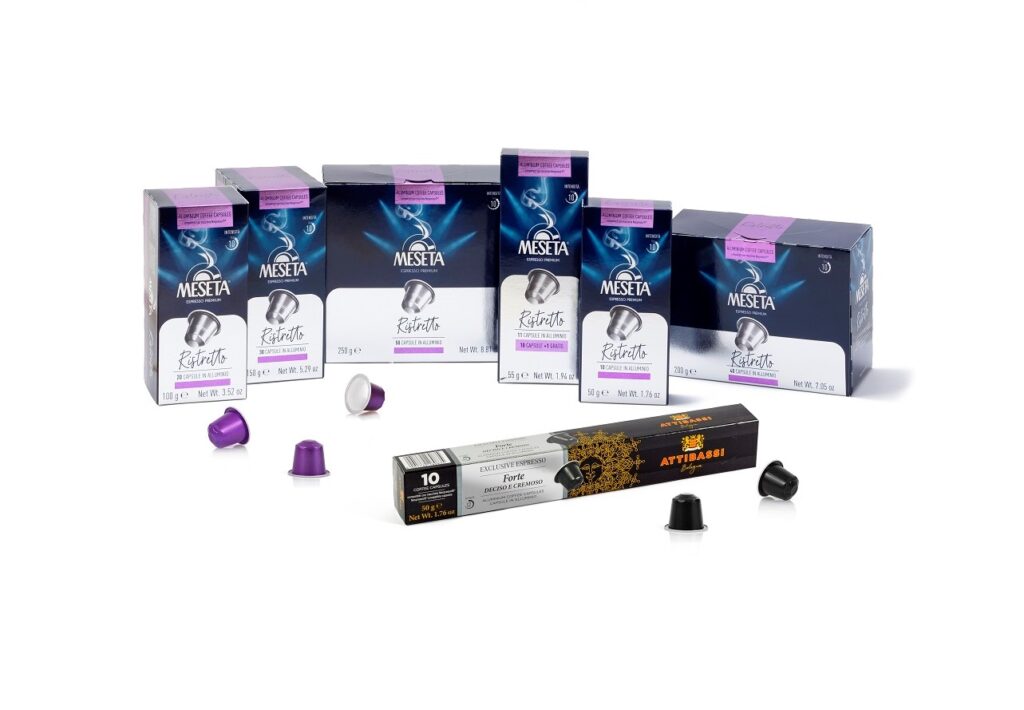
What were the production requirements, in terms of product type and production capacity, that led Coind to choose IMA as a partner?
Given the complexity of the coffee capsule packaging process, we decided to turn to a world leader in the packaging sector, to have a reliable and structured partner able to take care of all the technical aspects of the process.
In fact, when packaging coffee, attention must be paid to various aspects. First of all, it is necessary to respect all the basic hygiene and health rules, which is added to the complexity of managing fine particles (the ground coffee inserted into the capsule). Plus, the machines must ensure millimetre precision in welding the top lid to the cup of the capsule, so that the latter is perfectly self-protected and the coffee inside keeps its organoleptic properties intact until the moment of consumption.
At the same time, the machines must have a certain tolerance in terms of the size of the empty capsules: it may happen that they differ from each other by a few microns, and this must not compromise the efficiency of the line.
Talking about efficiency, is there any data you can share? How do IMA’s machines and lines achieve high standards of efficiency?
The IMA filling machine is capable of producing 450 capsules per minute. If we think that on average every Italian drinks 4 coffees a day, IMA machines pack the annual quantity of coffee per capita in just over 3 minutes.
To make another comparison, one year of production of a single machine (potentially equal to over 236 million capsules) could satisfy the coffee needs of the whole of Italy.
This high standard of efficiency is achieved thanks to the use of fully automatic machines, which make it possible to minimise downtime due to the human component.
Based on your growth target, do you foresee an increase in capacity that could involve IMA?
The challenge of the next few years will not only be to better manage the workload on the production lines, but also to reduce their consumption and intervene in real time on anomalies. This is why we are developing a real-time performance monitoring solution together with IMA, using machine learning algorithms. A complex project, which is part of the production efficiency process undertaken by Coind, aimed at improving the management of our plants and increasingly reducing our environmental impact.
For further information visit www.coind.it/en/ and www.ima.it