MINNEAPOLIS, U.S. – From June 15-19, 2020, Bühler will host Bühler GO!2020. This virtual networking and engagement event supports Bühler’s efforts to build and strengthen an industry-wide collaborative network of food industry leaders, addressing global nutritional challenges such as sustainability, food security, and feeding 10 billion people by 2050.
Discussing and exploring latest food trends, such as alternative proteins and ancient grains with US and worldwide customers, will help ensure that companies have the agility and innovation power to effectively deal with the challenges put before them.
To support that, Bühler will open its brand-new Food Application Center in Minneapolis, Minnesota, on June 19. “Bühler GO!2020 is about learning together how the food industry can meet these global challenges with good sustainable businesses that create real impact,” says Andy Sharpe, CEO Bühler North America. Bühler GO!2020 will open its digital doors from June 15-19 at: Bühler GO!2020.
Together with its customers and partners, Bühler is supporting the evolution to a sustainable food industry. Bühler GO!2020 will further strengthen Bühler’s collaborative approach to today’s challenges for the food industry, by bringing together more than 500 leaders of food companies, academia, industry associations, government organizations, and start-ups.
Culminating in the opening of the Food Application Center in Minneapolis on June 19, the Bühler GO!2020 event will focus on framing the global challenges, creating safe and transparent food chains, sustainable protein supplies for 10 billion people, workforce development, and leadership.
“This new Food Application Center will be an important resource for the North American food industry as we focus on the future of food, reintroducing ancient grains, peas, and lentils into our diets, and innovating around plant-based proteins; all of this addressing the demands of consumers as diets are changing fast,” says Stefan Scheiber, CEO at Bühler Group.
“Many of the global challenges we faced before the coronavirus have only been intensified. Our collective situation has held a magnifying glass to these challenges. It has shown us where we can improve our food supply chain, and our ability to safely and sustainably nourish our population.”
To rise to these challenges, Scheiber expects great solutions to be developed with Bühler’s customers, “as it is here that we can marry the highly entrepreneurial American spirit with the best of our Swiss heritage as a high quality solution provider for world-class products. This event allows us to stay in close contact and enables companies to learn best practice from one another.”
At the one-week-long Bühler GO!2020, nearly 50 speakers from the food-processing industries will give expert insights, best practices, and inspiration for its 500 attendees hailing from 17 countries. Not only does the virtual event eliminate travelling time, Bühler estimates that GO!2020 saves around 400 tons of greenhouse gas emissions compared to a physical event, equivalent to the compensation output of 16,000 trees.
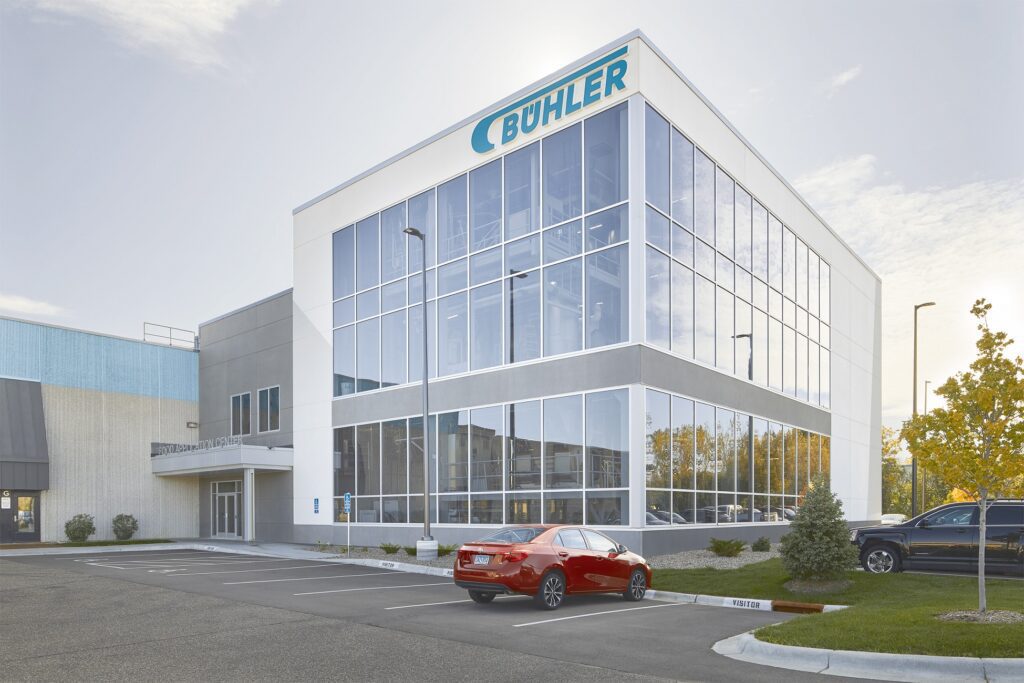
Resilience and collaboration
“We want to show our customers that they can rely on us even in times of crisis, be it for new product developments, for servicing their solutions, or when digitalizing their plants for the new normal we are now learning to live in,” says Scheiber. Bühler GO!2020 highlights the topics of resilience and collaborative innovation. The company has gone digital to support customers in their endeavors. With digital capabilities underpinning a service portfolio increasing yield and capacity, ensuring consistent product quality, providing remote support and reducing unplanned downtime, waste, and energy consumption, Bühler can support its customers efforts to deliver the strong demand they experience today while securing their operational results.
In short, Bühler’s digital platforms, myBühler and Bühler Insights, will support business resilience by enabling physical assets to consistently deliver highest performance. “Our portfolio of digital services has increased our capability to support our customers through good and bad times and underpin industry resilience. Over this week, our partners will see that collaboration is a key topic. It is only through collaboration that we, as an industry, can create the needed solutions to mitigate the climate crisis,” says Ian Roberts, CTO at Bühler. Bühler aims to reduce waste, energy, and water consumption in its customers’ value chains by 50% by 2025.
Food Application Center opening on June 19
The Food Application Center (FAC) will be the new Bühler stronghold in developing economically viable and sustainable food solutions in North America. The future solutions developed there will help feed a growing population of nearly 10 billion people in 2050. A unique installation, the FAC is a playground for the food industry.
“Innovation remains the lifeblood for sustainable market success, particularly in the food industry,” says Yannick Gaechter, Director of the new FAC. “New food opportunities are multifaceted and need to be addressed with partners across the whole food value chain. This is where the new FAC comes in,” Gaechter adds. “With the FAC, Bühler is helping to create an innovation ecosystem by providing predominantly North American food companies, start-ups, and academic partners with a platform and the capabilities for creating new products and processes that will help address – from farm to fork, and from bean to burger – not only the current consumer trends, but also our global nutrition challenges in a sustainable way.”
Drawing on 160 years of food processing expertise, the new FAC was created as a platform for developing new ways to transform peas, beans, corn, pulses, oats, ancient grains, and many other crops into new food solutions such as flours, snacks, pasta, cereals, and a myriad of extruded products, including plant-based meat analogues. Bühler will share more details on the Food Application Center’s capabilities at its opening at the end of next week.
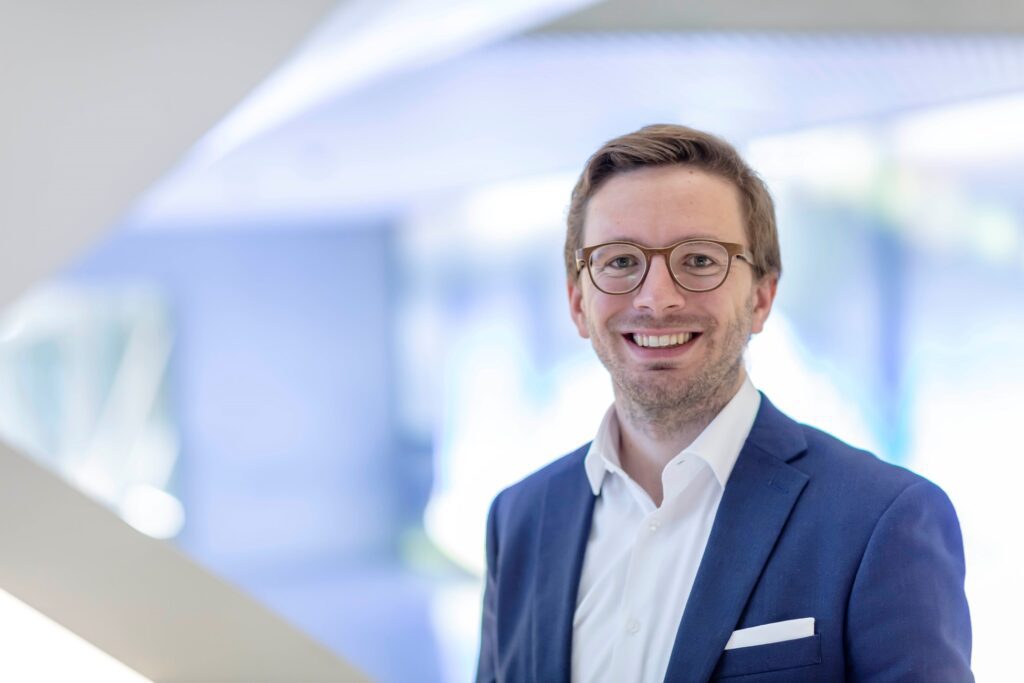
What is on show at Bühler GO!2020
During Bühler GO!2020, the company presents ChocoX, a new highly flexible, modular solution for chocolate moulding. Following a “plug-and-produce” concept, the new moulding line, ChocoX (pronounced “Choco Cross”) marks a breakthrough in the industry with its consistently modular approach. ChocoX can be installed on site within a week, reducing implementation time by 80%. ChocoX slashes the time for a line expansion by half, compared to previous solutions. Its modular structure allows for great flexibility. Modules can be changed or cleaned in as little as 30 minutes, and rearranging the process chain only takes between 30 to 120 minutes.
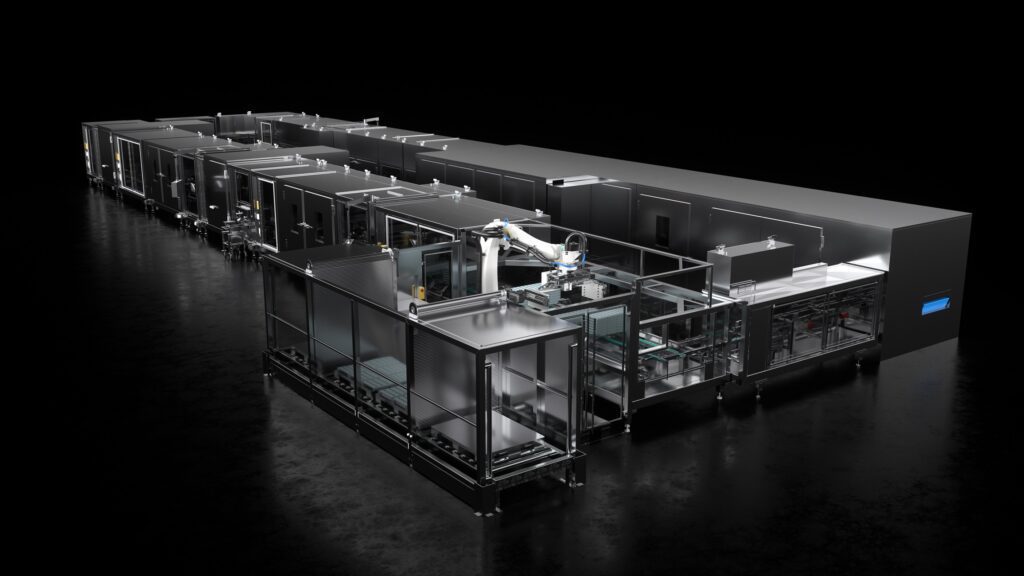
Customer services at the click of a button
The myBühler portal offers customers 24/7 access to all the information relevant to their technologies and equipment. myBühler streamlines the purchasing process with pricing and material information and online ordering. But it is far more than a standard customer portal. It is the starting point and the one-stop-shop for all digital solutions, including product information, e-Maintenance, e-Training, and e-Service such as Bühler’s Remote Guidance. Smart glasses enable Bühler’s specialists to instruct professionals at customer sites remotely. And Bühler guarantees first-level-support within two hours.
Education and training capabilities for Bühler customers
The Food Application Center in Minnesota, in addition to Bühler’s five other Application Centers in North America, also seeks to fulfill an educational role by providing the tools necessary for customers and partners to respond to a market characterized by rapidly changing trends. They are a place to learn about and innovate around topics such as nutrition, food safety, digitalization, sustainability, and mobility.
Bühler also introduced one of the first apprentice programs in the US. Now in place at three US sites, Minneapolis (Minnesota), Holland (Michigan), and Raleigh (North Carolina), 30 apprentices are currently in training. So far, more than 80 American apprentices have graduated from Bühler North America apprenticeship programs, with no educational debt and started ambitious careers in the industry, a sector that yearns for young workers with high class and relevant training.
Bühler North America was one of the first locations where Swiss apprentices were able to complete part of their training – including virtual classes, which they could follow despite the time difference. Since 2013, 31 young adults from Switzerland have completed part of their vocational training in the US. The benefits of this approach are obvious: Apprentices gain a first-hand experience of different cultures and languages. They enhance their professional and social skills, broaden their minds, and become fit for a job in the international labor environment that Bühler offers.
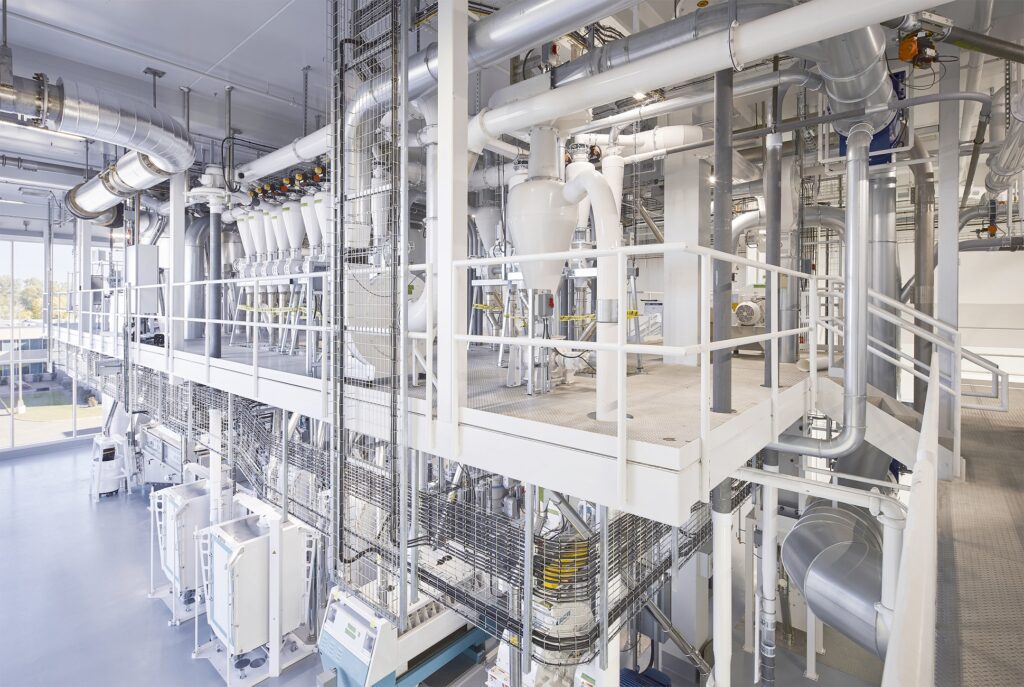
Bühler North America supports food and mobility customers since 1957
With the foundation of 160 years of Bühler innovation, the Minneapolis installation is the go-to solution provider for North American customers eager to develop new food solutions. Six application centers – including the now officially opened Food Application Center – and more than 850 employees ensure that customers throughout the Americas can develop and produce foods ranging from sweet temptations such as wafer creations, cookies and chocolate, to staples such as flour, pasta, breakfast cereals, meat alternatives and pet food according to highest food safety standards – 24/7. With sales offices including those in Raleigh (North Carolina), Richmond (Virginia), Holland (Minnesota), Stockton (California), Owatonna (Minnesota), Toronto (Canada), nine service stations, and three manufacturing sites across the country, Bühler North America has contributed 16% of Bühler’s 2019 overall turnover of CHF 3.3 billion, serving nearly 8,000 customers.