UZWIL, Switzerland – Bühler’s new ChocoX is as flexible as its pronunciation “Choco Cross”. The solution combines flexibility and agility in production and hygienic design, resulting in significantly lower operational costs. Its completely modular design allows for unlimited crossovers of the process line and quick adaptation to different products.
Every function of the line is placed in an independent module, to be freely adapted for the production process customers need.
In under 30 minutes, chocolate producers can change a module. “With the new ChocoX, customers are able to react quickly to changing consumer tastes and market trends – while reaching new heights in efficiency,” says Fritz Dorner, Head of Business Unit Confectionery.
Several patents are currently pending for this new state-of-the-art moulding solution. Bühler will share more information on its commercial use by the end of 2020 or the first quarter of 2021.
Where refitting of a moulding line used to take more than a month on site, Bühler offers a significant time reduction. An entirely modular approach led to a line arrangement that can be used almost like a toolbox. Each module of the new ChocoX is built on wheels.
This allows for easy reconfiguration of the sequence and, thus, more product variety. Arranging new processes only takes 30 to 120 minutes depending on the sequence changes. Thereby, more individual recipes will see the light of day with just one production line.
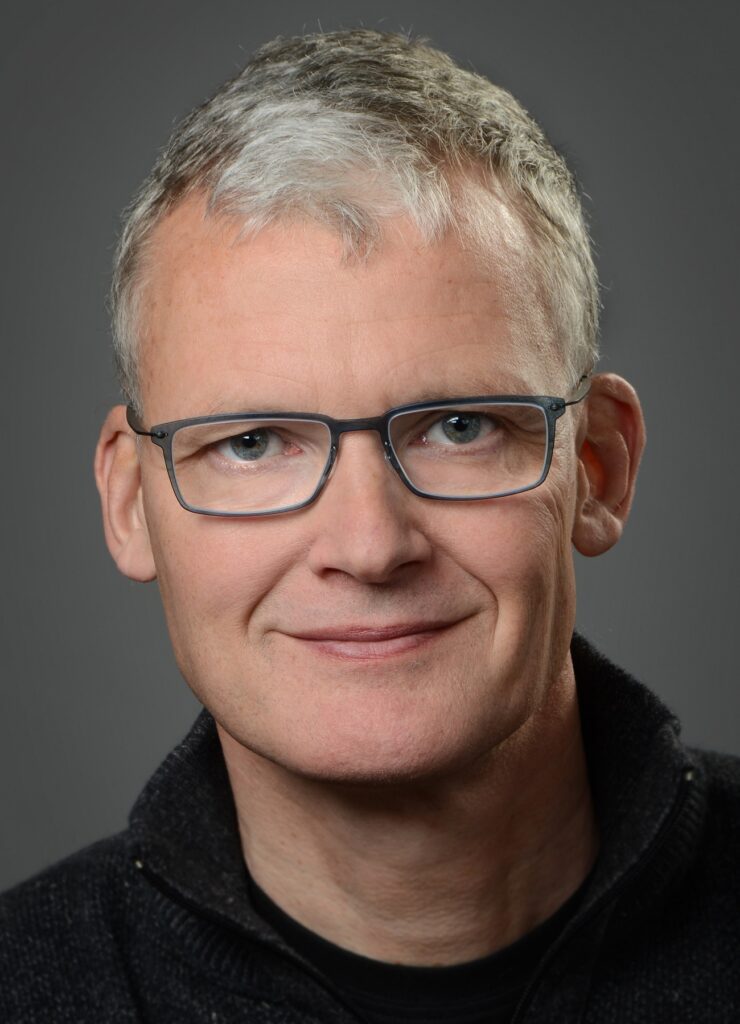
Plug and produce with a combination of performance and sustainability
Together with its customers, Bühler can set up the new ChocoX and launch its operation on site within one week. Thanks to standardized self-contained modules, assembling and removal of each module takes less than 30 minutes.
And line extensions are ready in half the time than other solutions. The delivery of standard modules is three to five months, with an implementation on site of just 24 hours.
The new ChocoX comes with a reduced footprint thanks to integrated control boxes that replace all central switch cabinets. Optimized shaking modules shorten the shaking time and the decreased cooling volume adds to the line’s lower energy consumption.
Integrated buffering, automated mould handling
The new ChocoX is unstoppable – in the truest sense of the word. Bühler has included a highly efficient buffering system. This makes the extension with an external buffering system obsolete and offers exceptional cost advantage from day one.
In addition, the process keeps the important thermal consistency at an ideal level, including the transition to packaging. The smart buffering reacts to the packaging output, so the new ChocoX can keep running even during a stop in the packing process. The fully automatic mould handling system further increases the line’s efficiency.
“There is no more need to carry the heavy moulds. The handling system simply distributes the moulds automatically for you,” says Fritz Dorner. And it is only one of the line’s highlights that reduce operation efforts.
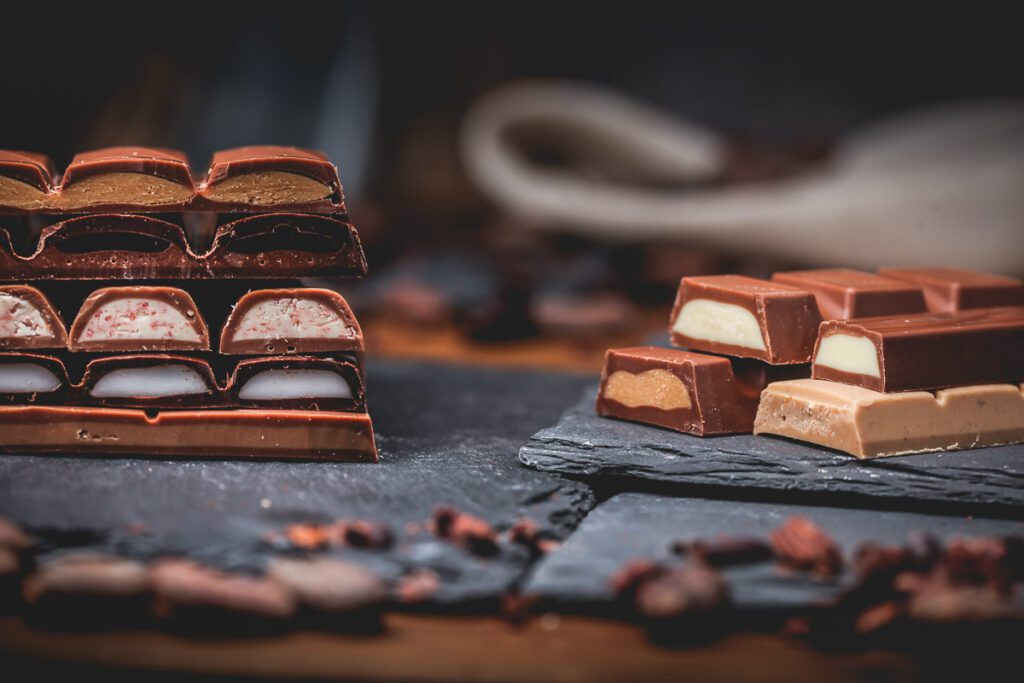
Much more uptime thanks to less cleaning and maintenance
Moulding lines are prone to getting dirty quickly and often they are hard to access. With the new ChocoX, however, Bühler sets new standards also in terms of hygienic design. All modules work without chains. In addition to increased food safety, the chainless line design lowers the maintenance efforts. Generally, cleaning time per module is only 30 minutes, also because there are no installations underneath the depositing sections.
“Large doors offer free accessibility to all modules from the front and the back,” says Frank Huperz, Head of Design & Engineering. The new ChocoX lets you take out the depositor and demoulding internals which are normally hard to reach. The demoulding section, for example, comes with an extendable quick-change system on wheels.
In general, “depositing tool changes can be done while the modules are running empty – with a highest level of safety,” Huperz adds.
Finally, also the cooling coils offer easy access from both sides. The completely new cooling technology relinquishes the complicated, hard-to-clean and voluminous Paternoster system. Thus, the new ChocoX provides for a considerable reduction of downtime thanks to less cleaning and maintenance efforts needed.
Bühler is looking forward to discussing further details regarding its commercial use by the end of 2020 or the first quarter of 2021.
For more information on Bühler’s moulding solutions please go to: https://www.buhlergroup.com/content/buhlergroup/global/en/process-technologies/Moulding-and-Forming.html