SANT’AGOSTINO, Ferrara, Italy – Whether designing a new roasting facility, expanding, or optimising an existing one, green coffee processing plays a crucial role in overall production efficiency. Throughout the entire roasting process, tailored reception, storaging and handling systems are critical areas for implementing the business continuity plan, avoiding any downtime and maximising plant effectiveness.
By Cosimo Vitale, Head of Engineering at IMA Coffee Petroncini
The growing reliability and effectiveness of these solutions have seen Petroncini confirmed in 2020 as the supplier of green coffee processing solutions by one of the leading coffee companies present on the market today.
A history devoted to coffee
Throughout the company’s 100 years in business, sound experience and ongoing research have been concrete elements in the evolution of the latest technologies and engineering solutions applied to green coffee reception and processing plants. Over the years, Petroncini R&D has come up with solutions able to achieve the highest level of efficiency, productivity and safety, combined with maximum attention to coffee integrity, for any requirement, plant capacity and processing line.
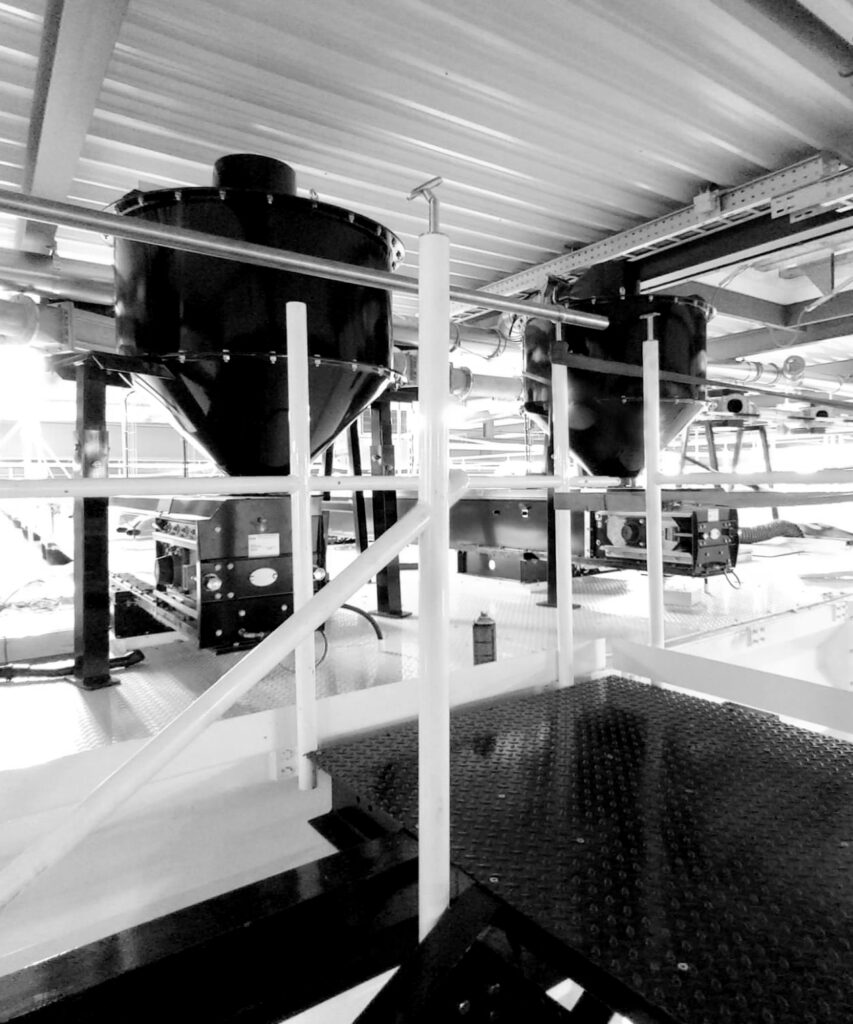
Strategic engineering for every processing plant
Considering plant capacity and optimisation of handling operations, every customer can decide the preferable way to receive and treat the raw coffee in their facilities.
“A suitable storaging solution should consider the number of coffee origins that will be used during production and the desired storage time, be it in storaging silos or in the warehouse. The above considerations always depend on the availability of space.” tells Cosimo Vitale, Head of Engineering at IMA Coffee Petroncini.
“A tailored engineering solution should combine customer logistics needs and production expectations with the available space and budget. The ability to be a reliable partner for a coffee company strongly relies on the combination of these key points” he affirms.
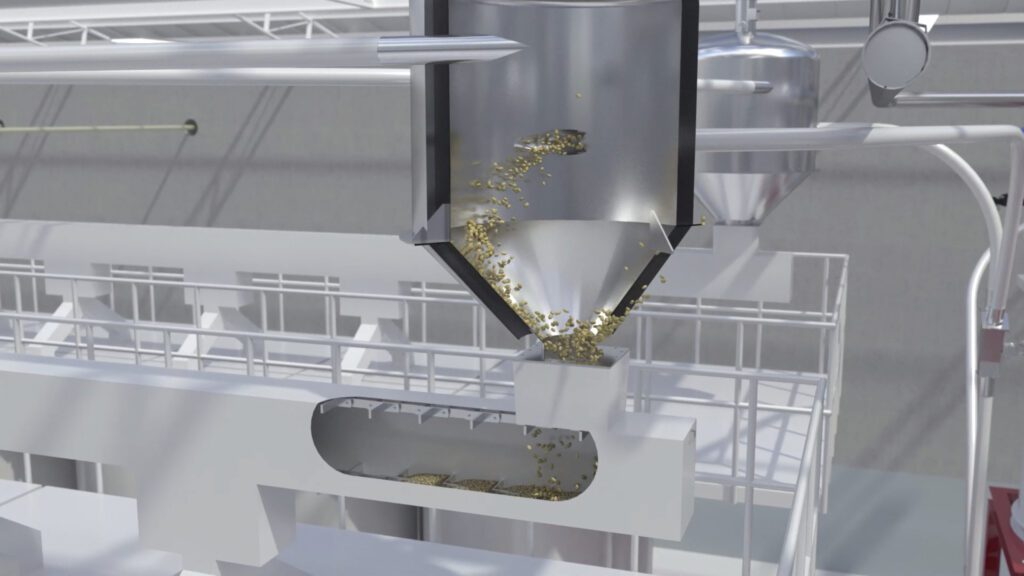
From the premise to the final project: A Case Study
One of the biggest coffee processing companies on the market today wanted to increase its green coffee processing and handling capacity. It turned to Petroncini to design and provide a green coffee processing plant complete with reception station for big bags, a handling system, chain conveyors for horizontal coffee handling and conveying, and more than 100 modular block silos for a total capacity of 1,500 tons, with special valves for product dosage.
“Responding to the customer’s need to store the coffee in a new section of the plant, Petroncini provided a reliable and efficient solution for rapid big bag discharging. Thanks to a special engineering solution, big bags can be placed on a special cutting device with knives, so that the coffee can be quickly discharged into a hopper combined with a weighing system. This reception station can discharge up to 20 tons per hour of green beans, and it is extremely safe for the people involved in the bag unloading operations” Vitale explains.
“The hopper has been specifically designed for rapid big-bag discharging and is equipped with the most advanced aspiration system for receiving green coffee in big bags. The integrated dust extraction system under the walkable grid optimises aspiration efficiency by exploiting all of the available surface. The air flow can be directed through suitable piping to the main dust filtering system” Vitale reveals.
In green coffee processing plants, conveying equipment links the various processes into complete production units. Even if conveying in itself does not add value to the coffee, an effective conveyance system plays a critical role in the overall energy-efficiency of the operations, avoiding any downtime and ultimately optimising productivity.
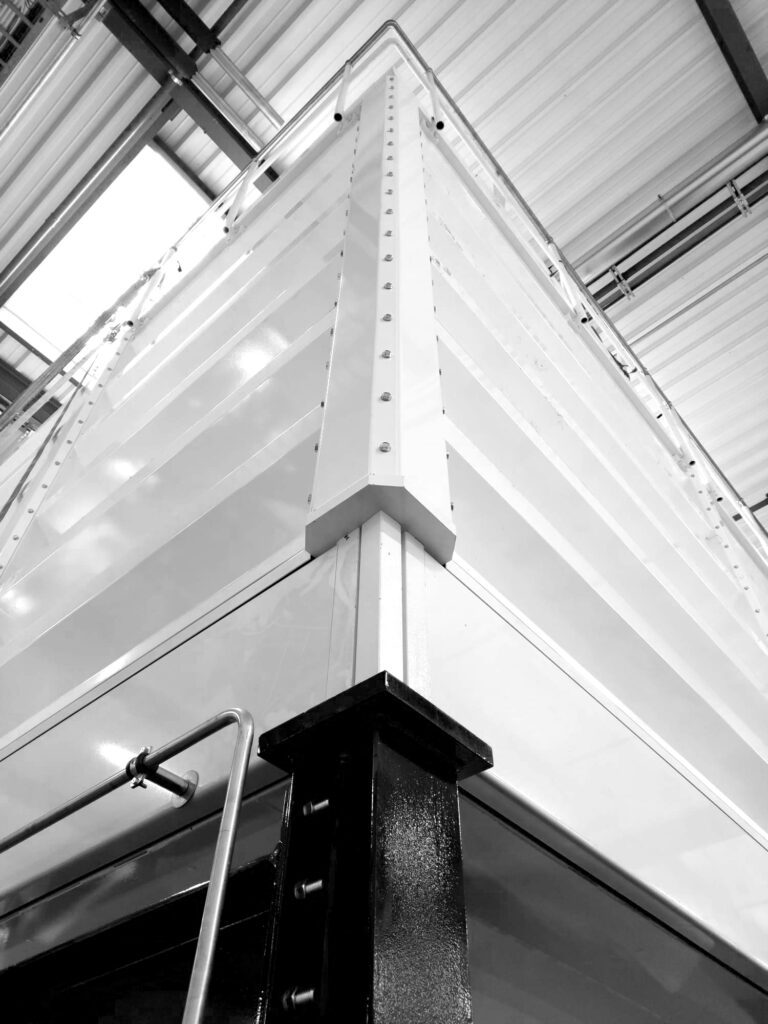
A reliable and efficient conveying system
“Nowadays, companies are paying more and more attention to coffee quality. A good conveying system, even in a green plant, can guarantee the highest preservation of product quality, avoiding any contamination thanks to its Hygienic Design specifications.” Vitale says.
“In this project, the limited of height space and several restrictions due to the layout of the premises, meant the pressure pneumatic conveyor was the most flexible solution for loading the receiving cyclones above the silos, avoiding the existing equipment and structures along the way.”
The mechanical chain conveyors, each 40 metres in length and with a total handling capacity of 20 tons per hour, allow for an accurate and extremely hygienic discharge of the raw beans into the modular squared silos.
“The choice of the modular block layout for the silos was strategic. The modular shape allows for total optimisation of the vertical space and also makes it possible to rapidly expand the storaging capacity” says Vitale.
LINE-S Valve
The engineering solution provided by Petroncini for green coffee handling from the silo to the destination was particularly successful from several points of view.
“The optimisation of space was a very important factor right from the beginning of the engineering studies, and the solution applied to the dosing process was the cornerstone of the entire project. The suction pneumatic conveyor, combined with the special LINE-S dosing device, has been engineered and developed by Petroncini to maximise energy-efficiency and cost-effectiveness in certain plant layout conditions” Vitale explains.
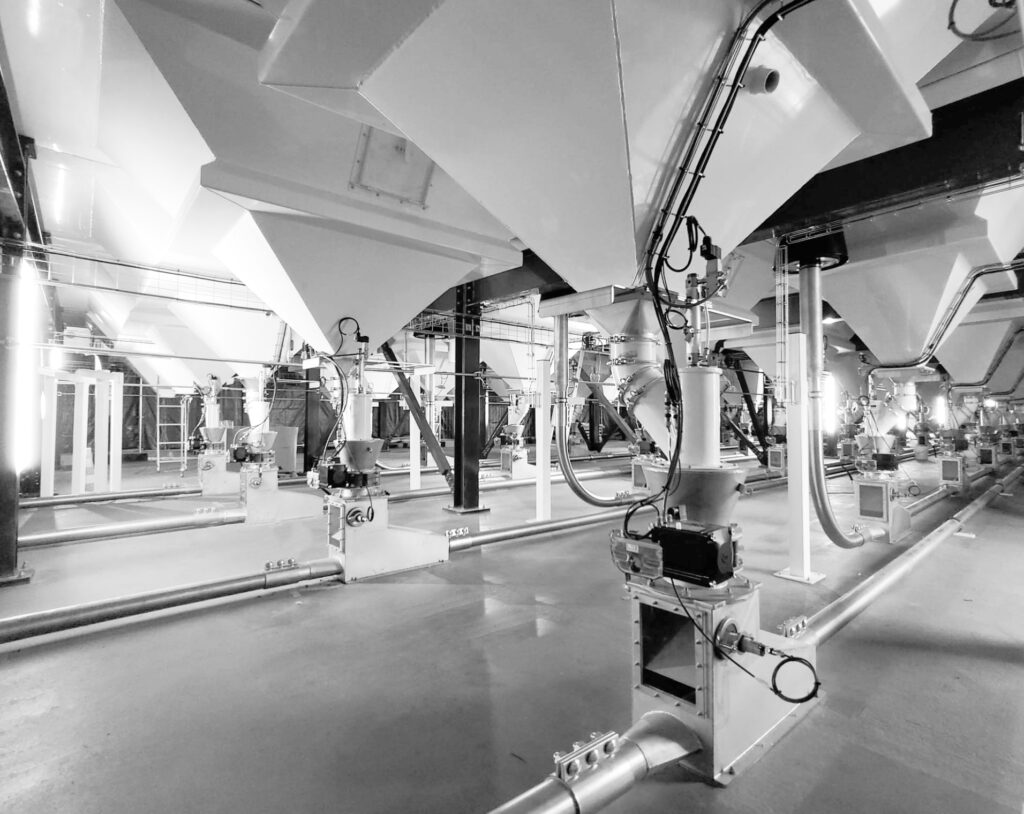
LINE-S is an effective solution for green bean unloading from silos and, in a minimum amount of space, can combine several accessories for product loading, dosing and conveying, complete with sensors for system control.
“Due to its smaller space footprint compared to other common valves, the use of LINE-S dosing valves meant a lot of vertical space could be saved, so that it was possible to gain 0.5 metres in height for each silo, corresponding to an additional storaging capacity of 150 tons” Vitale affirms.