MILAN – Cappac recently opened a state-of-the-art, high-capacity production facility in The Netherlands, processing Private Label for Aluminium Nespresso-compatible. Together with strategic business partners, the company will supply (food) retail, foodservice and coffee roasters with high quality Aluminium Nespresso-Compatible capsules globally. The fully automated and robotised CAPPAC facility is equipped with the latest innovative IMA Coffee filling and packaging machines.
With a one-billion annual production capacity, the Dutch company will become one of the largest Private Label producers in the market.
Single-serve capsule fillers are core solutions of the IMA Coffee Hub, featuring key attributes developed over the years to ensure significant flexibility.
A comprehensive range of equipment provides high, medium and low-speed solutions to answer 100% of market demands. Ground-breaking, high-performance, flexible solutions are available to process any single-serve capsule configuration present on the market today.
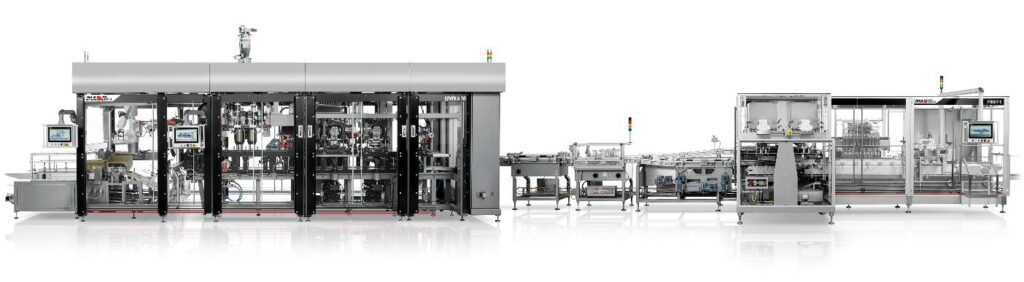
Ready to leave the production site, coffee capsules benefit from cutting-edge secondary packaging solutions for product integrity and top-rate protection right through to delivery.
Together with its close attention to the needs of the customer and to the trends which influence the market, IMA can provide the coffee processing and packaging industry with turnkey production lines designed to maximize productivity and enhance product quality.
2020 marked the start of IMA’s close collaboration with CAPPAC in view of supplying a fully automated, complete packaging line for Nespresso®-compatible aluminium capsules. Careful evaluation of the customer’s needs and the ambitious targets set by CAPPAC led IMA to opt for an integrated solution consisting of the brand new UNIKA modular capsule filling and sealing machine together with FTB577-C, a highly flexible cartoning solution. The line, including a robot feeding system ensuring gentle handling of the aluminium capsules, currently reaches a production speed of 600 capsules (60 cartons) per minute.
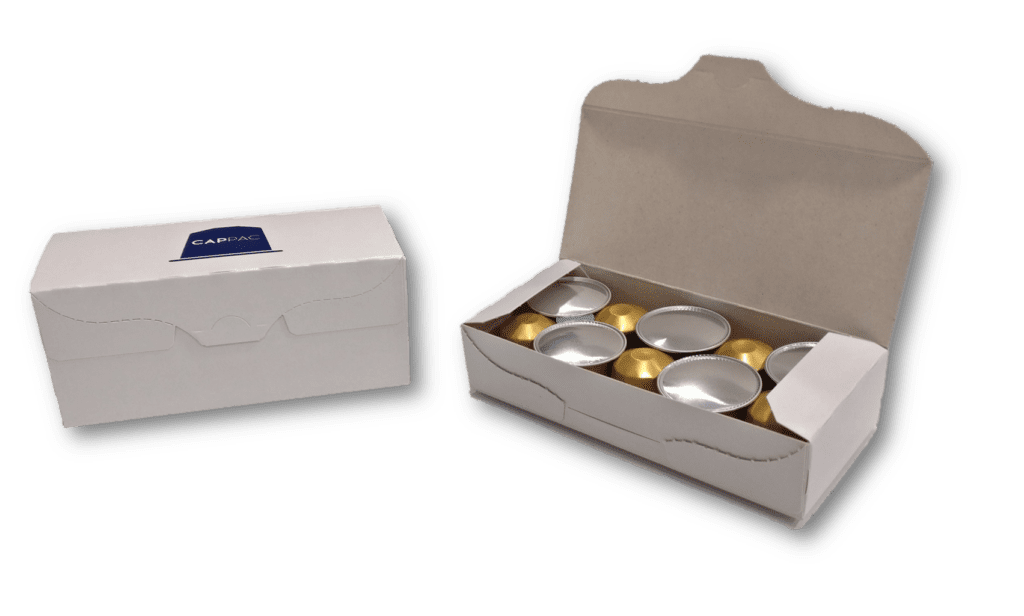
We asked Bas de Vet, Chief Capsule Officer, Owner and Founder of the company, a few questions to illustrate the project and understand his views of working with IMA.
What were your main objectives for this new project?
Let me say that there was one overriding objective: CAPPAC wants to become the largest producer of Private Label aluminium Nespresso-compatible capsules in the world. The first step entailed sourcing the best certified coffee together with our strategic partners.
What specific needs came top of the list?
Clearly we needed top-class equipment. Productivity levels were priority and we discovered IMA was the ideal choice for high-speed processing. Plus they were able to deliver a turnkey solution for complete lines including primary and secondary packaging of Nespresso-compatible aluminium capsules. This convinced us and we are still convinced.
Now that the line is running, what are the main benefits?
The UNIKA-FTB577-C line does exactly what we expected. It’s great to have such reliability and top performance at such high processing speeds. The line is fully automated and handles up to 600 capsules per minute.
How was the integrated line configured?
Capsules are fed into the UNIKA filling machine by KUKA, the robotised depacker. It picks the rows of aluminium capsules from the carton and places them into the machine’s destacking unit. UNIKA then fills each capsule and this is one point I want to stress: dosing precision and uniformity of coffee with different densities are obtained thanks to an integrated sensor.
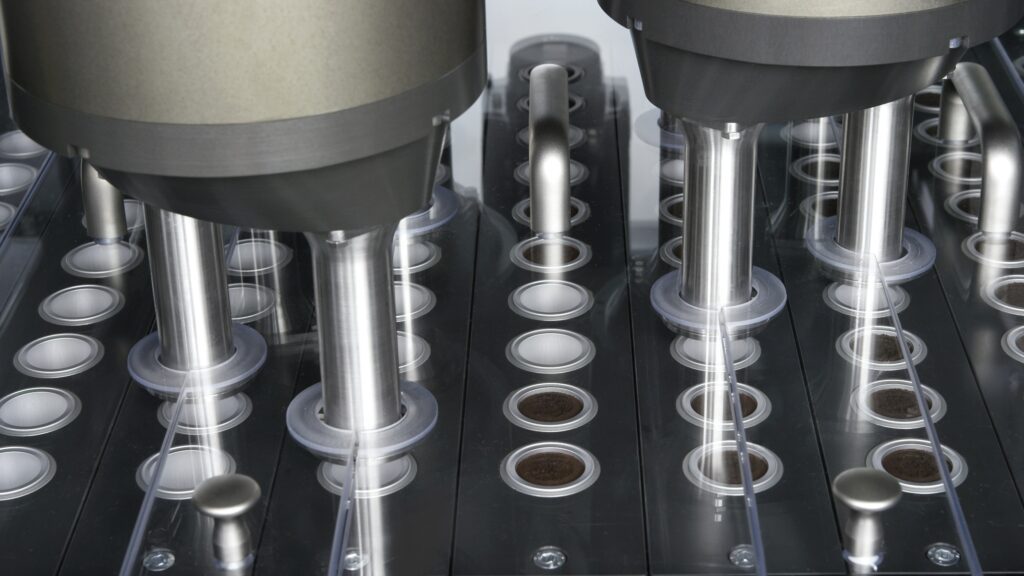
Then, as the FTB577-C cartoning machine is the natural extension of the filler, IMA developed a customised capsule transfer system, paying close attention to gentle handling needs to avoid damaging the aluminium capsules.
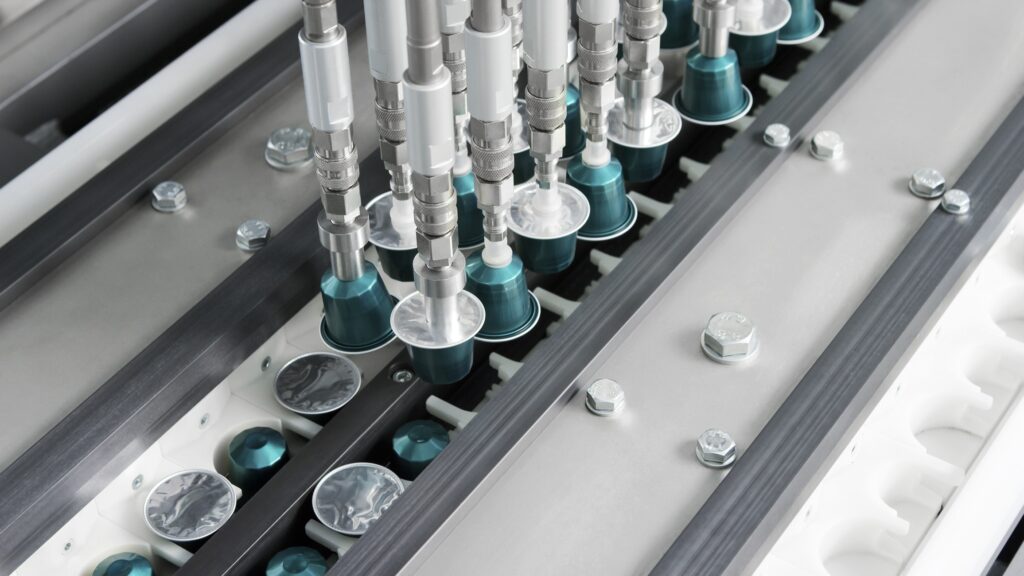
Our operators quickly got used to the user interface which is one for both machines. The HMI displays data with production statistics, notifications regarding planned maintenance requirements, warnings and alarms, including prompts to solve issues without calling maintenance teams.
How have IMA solutions responded to CAPPAC ’s needs?
We found it important and a huge benefit being able to speak to a single supplier for the entire line. This led to fast replies whenever we had a question and close attention to our requests. Timing issues are also much easier to coordinate, everyone you speak to is focused on your key objectives, and consistent quality and shared knowledge are guaranteed. We feel in excellent hands and will undoubtedly benefit from this partnership.
Considering CAPPAC’s production trends/volumes, how efficient is the IMA line? The modular structure of the filling machine and the easy accessibility to the whole line a llow quick intervention for maintenance and definitely avoid unwanted downtime. Moreover, thanks to KUKA, the robotised depacker, there is no need for a technician to load the capsules. This enables an operator to devote their time to more valuable tasks. So, in the end, I am pretty sure we will reach our target volumes thanks to the reliability and the high speed of the solution supplied by IMA: one billion capsules per year.
Are there any more projects in the pipeline?
Yes. We are planning to expand operations with four more lines fully equipped with IMA capsule filling and packaging technologies.
Discover IMA COFFEE Processing and Packaging solutions at www.coffee.ima.it