REINBEK, Germany – The Canadian coffee roaster Café William is consistently strives to significantly reduce the carbon footprint of its products through sustainable, ecological commitment across the entire coffee production chain. An important step in this direction is the new roasting factory, which is equipped with an electrically powered roaster. The new production facility of Canadian coffee roaster Café William was officially inaugurated on 7 February 2024.
“It was a great, very transparent collaboration with Neuhaus Neotec. And what we have achieved together has exceeded our expectations. For a few weeks now, we have been roasting purely electrically with electricity from hydropower,” says Rémi Tremblay, CEO of Café William.
First industrial plant to roast coffee completely CO2 neutral
The electrically powered RFB roaster with an hourly output of 3 – 3.5 t of green coffee requires a maximum power supply of one megawatt, which is roughly equivalent to the output of four Super Charger charging stations for electric cars.
By roasting with green electricity instead of gas as an energy source, greenhouse gas emissions can be significantly reduced. If the roaster is powered by green electricity from renewable sources, as in the case of Café William, roasting is even a completely CO2-neutral process.
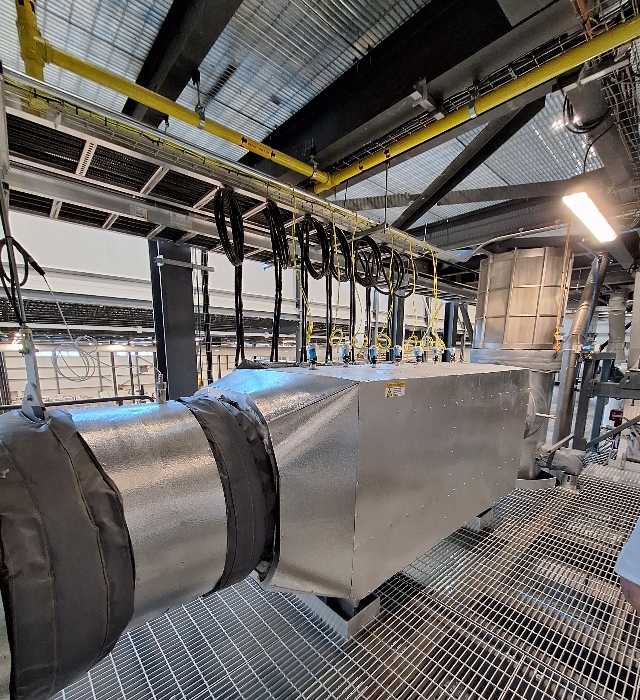
If a customer wants to keep several heat energy source options open, Neuhaus Neotec has designed this RFB as a dual-energy hybrid roaster, which can be operated both purely electrically and with natural gas. If required, it can even run on both energy sources at the same time, e.g. to buffer high energy peaks using one or the other energy source.
Reduce energy consumption, increase efficiency
The system design of the RFB roaster series enables the use of purely electrical energy for roasting as well as the use of other alternative resources without significant structural modifications. In hybrid operation with gas and electricity, the system is simply expanded to include an additional heat source.
Thanks to continuous optimization of the process control and system design, the roasting process with the RFB is particularly energy efficient, regardless of the heat transfer medium.
Due to the use of economical drives and components, high efficiency in the utilization of thermal energy, the low heat losses due to optimum insulation and the high recirculation rate in the roasting gas circuit, the RFB roasting systems from Neuhaus Neotec are characterized by significantly lower energy consumption compared to conventional roasting technologies.
Uncompromising when it comes to quality
One of the great strengths of the RFB is its high flexibility and wide range of roasting profiles. Even when using electricity (or hydrogen) as a heat source, roasters can continue to use their proven roasting profiles. “Initially, we weren’t entirely sure whether these energy sources would offer the same flexibility in temperature control as natural gas,” explains Dr Stephan Sternowsky, Head of Technology at Neuhaus Neotec.
Sternowsky continues: “However, the extensive roasting tests in the field have shown us that roasting with electricity allows the same scope for design as with gas and that roasting curves are just as reproducible.”
The German manufacturer also has good news for coffee roasters who are already roasting on RFB systems: With a manageable amount of effort, many existing systems can be converted to electric or hydrogen operation.